SEAMLESS ITR FLEXOGRAPHY
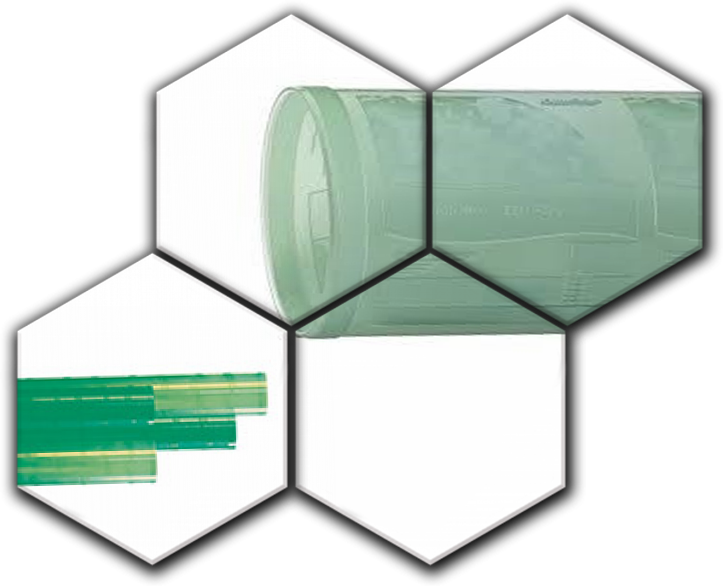
Designed for Flexographic printing, seamless ITR (In-The-Round) sleeves are ready-to-image synthetic photopolymer sleeves designed for mounting outside the press, after the design extrusion has taken place and are ideal for conventional plate mounting.
USES
Business forms, packaging for food and drink, corrugated carton material as well as other flexible subtrates such as, label, envelopes, wallpaper, wrapping paper, newspapers, textiles, fiol, etc.
APPLICATION
- ITR Flexo printing for short- and long runs, as well as standard- and high-quality printing.
- Business forms, packaging for food and drinking products, and corrugated carton material.
- Other flexible substrates: labels, envelopes, wallpaper, wrapping paper, newspapers, textiles, foil, etc
MANUFACTURING PROCESS
- Pre-manufactured from various materials like thermoplastic composites, thermoset composites, and nickel.
- A continuous sleeve with a seamless layer of photopolymer is topped reserveda LAM coating, ready for imaging, exposure, and processing.
- Thin’ sleeves are created without foam or cushioning to be thrown away after use to keep costs low.
- Long-run, reusable sleeves with a foam or cushion base are used for very high-quality printing.
- Most sleeves are processed in solvent chemistry processors.
TECHNICAL PARAMETERS
Sleeve types : Classic/Thin/Ultra Thin
Material : Synthetic Photopolymer
Sleeve thickness : 1.570~3.165mm
Variable Wall thickness : 1.254~3.961mm
TIR : <0.02mm
Maximum length : 1650mm
Recommended screen ruling : Dependant on sleeve type
Suitable adaptors/bridges : Cushion adaptor, bridge or standard steel-air-cylinder
Available screen technology : ESKO HD Flexo
Available resolution : Maximum 4000 dpi
Washout : Solvent-based/Water-based
ADVANTAGES
- Versatility allows for printing of a wide variety of porous or non-porous flexible substrates.
- High quality ink transfer with solvent based, water based, or U.V curable inks.
- Excellent print quality and low dot gain without distortion and skew errors.
- Easy and safe mounting allows quick turn-around time.
- Tight tolerances (TIR < 0.02 mm) allows for greater stability.
- Highly durable sleeves are water washable and easy to store, making for low maintenance.
- Lower cost compared to other technologies, with lower inventory and tooling costs.
DISADVANTAGES
- RETROFIT ABILITY: Cost of retrofitting cylinders to older press equipment can be slightly
discouraging, although nearly any existing print cylinder can be modified for sleeve mounting. - HANDLING: Without the proper care, sleeves may experience reduced wear and cut resistance.
The thinner the base sleeve, the more careful the handling needs to be. - STORAGE: For high-quality repeat work, sleeve storage and cataloguing can prove challenging.
- COST: Sleeves typically cost more per square meter compared to flat plates but savings
associated with the elimination of mounting, higher press speeds, and greater run length
quantifies the cost. - TIME: ITR sleeves can take days to obtain, but lead times can improve as capacity increases.