CERAMIC ANILOX ROLLER
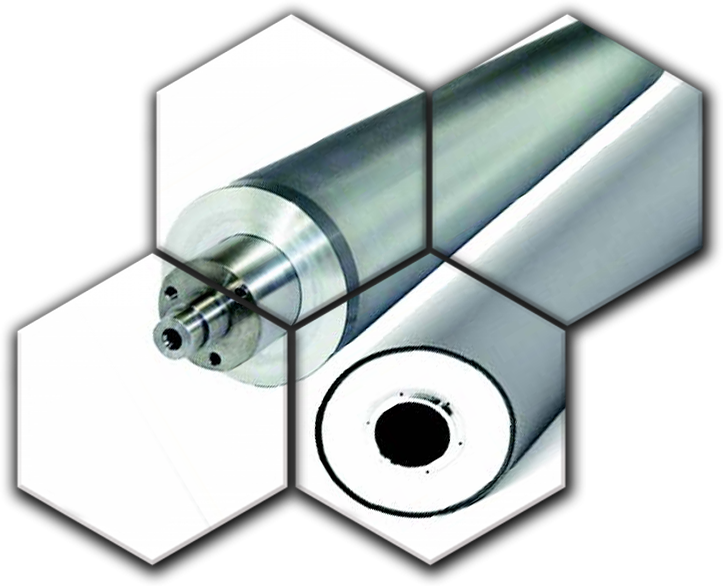
A Ceramic Anilox Roller is a hard cylinder that is usually constructed from a steel or aluminum core and then coated with an industrial ceramic coating before it is engraved. Various cell shapes can be engraved such as hexagon, quadrangle, lime cobra pattern, art pattern, etc. to meet the task requirement of modern-day print quality challenges.
USES
Labels, envelopes, paper forms, handbags, corrugated boxes, coated & wood-patterned paper products, glazing, wallpapers.
APPLICATION
- Flexographic, lithography, gravure printing, UV coating.
- Labels, envelopes, paper forms, handbags, corrugated boxes.
- Coated & wood-patterned paper products, glazing, wallpapers.
- Optical-, PE-, release-, and lithium battery diaphragm film, aluminum foil.
MANUFACTURING PROCESS
Each anilox roller goes through eight highly precise manufacturing processes to meet all relevant roller standards and deliver the highest quality anilox rollers for the perfect quality print.
- Base roller processing – all bases are made from quality hollow seamless tubes.
- Sandblasting treatment – ensures a good key on the surface for the first alloy.
- Nickel-chromium alloy coating – high bond surface with good metal affinity.
- Chromium oxide ceramic layer – working layer for anilox rollers is prepared using a plasma spraying system to reach an optimal hardness of approximately 1300-1450 HV.
- Carborundum grinding – silicon carbide stone is used to grind the ceramic surface.
- Carborundum polishing – micro-polishing with silicon carbide prepares the ceramic surface for engraving.
- Laser engraving – directly applied to the ceramic layer to allow for precise size and etch depth of each cell.
- Polishing and cleaning – to ensure removal of any “rough” edges and cell wall abnormalities.
We use the most advanced ALE optical laser engraving machines to ensure cell depth, smoothness, and consistency for even ink application and delivery across the entire roller face.
TECHNICAL PARAMETERS
Screen Scope : 20-1800 LPI
Diameter Range : 40-600mm
Maximum Width : 5000mm
Cell Shapes : See images below
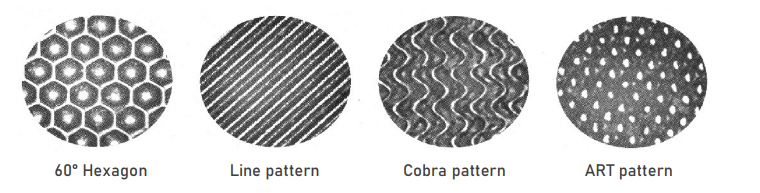
THINGS TO CONSIDER
When specifying an anilox roller, it is important to note what your specific requirements are.
Here are some helpful tips:
- What image is to be printed? (solid, line, halftone, etc)?
- What is the Anilox-to-plate ratio?
- What substrate is to be printed onto (porous, treated, top coated, etc.)?
- What ink system is to be used? (UV, solvent-based, or water-based)?
- How does the plate material respond?
- Plate mounting tape – Cushion mount?
- What are your press speed and drying capacity?